Explore the Latest in Industrial Electronic Equipment
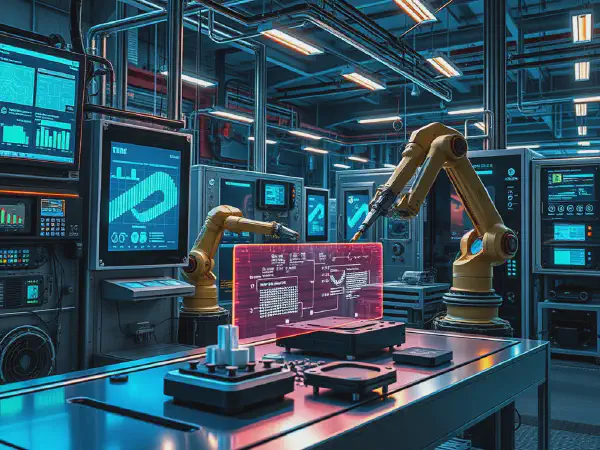
Understanding Industrial Electronic Equipment: A Comprehensive Overview
Industrial Electronic Equipment plays a crucial role in modern manufacturing and production processes. These devices encompass a wide range of machinery and systems used to monitor, control, and automate industrial operations. Examples include sensors, programmable logic controllers (PLCs), and robotic systems, all designed to enhance efficiency and precision in operations. The evolution of industrial electronic equipment continues to provide manufacturers with advanced tools to improve productivity, safety, and quality across various sectors.
Accurate data is crucial; using a temperature data logger ensures precision in environmental monitoring.
In today's competitive landscape, the importance of Industrial Electronic Equipment cannot be understated. These components are essential for driving automation in factories, leading to increased operational efficiency and reduced human error. Their integration into production lines allows for real-time data collection and analysis, enabling better decision-making and resource allocation. Furthermore, as technology progresses, the scope of industrial electronics expands, incorporating IoT and AI functionalities for smarter manufacturing solutions.
With the rk120-03 being recognized for its reliability, professionals trust it for critical industrial applications.
The need for Industrial Electronic Equipment is underscored by the constant demand for higher production rates and lower operational costs. With the ability to streamline manufacturing processes, reduce waste, and enhance product quality, these systems contribute significantly to the overall success of industrial operations. The ongoing advancements in electronic components, control systems, and automation techniques are reshaping industries to meet the growing expectations of a global market.
As industries continue to adapt to technological changes, investing in Industrial Electronic Equipment becomes increasingly vital. Companies are leveraging these advancements to not only stay competitive but also to address sustainability challenges through energy-efficient practices and sustainable manufacturing principles. The convergence of industrial electronics and digital technologies is paving the way for the future of manufacturing.
In summary, Industrial Electronic Equipment serves as the backbone of modern industrial operations, enabling automation, efficiency, and innovation. As we look toward the future, the integration of smart technologies into these systems will only enhance their capabilities, making them indispensable to manufacturing and production sectors.
Industrial Automation
Industrial automation refers to the use of control systems like computers or robots for handling different processes and machinery in an industry to replace human intervention. The role of sensors in industrial automation is paramount as they enable real-time data collection, which is critical for monitoring equipment performance and environmental conditions. Sensors like temperature, pressure, and proximity sensors provide valuable data that can lead to enhanced operational decision-making processes.
Programmable Logic Controllers (PLCs) are a cornerstone of industrial automation. They are designed to control various physical processes through programmable instructions, allowing for flexibility and efficiency in operations. The benefits of PLCs include ease of programming, real-time processing capabilities, and the ability to handle complex control tasks, making them essential in production environments.
Advancements in robotic control systems have revolutionized manufacturing practices. Modern robots are equipped with sophisticated software that allows for enhanced precision, speed, and adaptability in various tasks. These robotic systems can be programmed to handle intricate processes, and their integration within industrial environments helps in reducing labor costs while increasing overall productivity.
The innovative features of the hmp113 make it a top choice for modern temperature monitoring solutions.
Electronic Components
Electronic components serve as the building blocks for all industrial electronic equipment. Common types include resistors, capacitors, diodes, transistors, and integrated circuits. Each component plays a specific role in ensuring the proper functioning of electronic systems, from basic circuit design to advanced control systems.
Semiconductors hold tremendous importance in manufacturing as they are integral to the functionality of most electronic components. They allow for the control of electrical currents, making devices like microcontrollers and sensors viable in various industrial applications. The ongoing advancements in semiconductor technology are critical in meeting the increasing demands for faster, smaller, and more efficient electronic equipment.
Power electronics is an area witnessing rapid advancements, particularly in industrial applications. The focus on improving efficiency, reducing energy loss, and managing thermal performance is shaping trends in power electronics. With the rise of renewable energy and electric vehicles, industrial sectors are adapting power electronic systems to enhance their operations and meet sustainability goals.
Control Systems
Control systems are essential in maintaining the desired performance of industrial processes. An overview of control system design reveals that it typically involves defining system requirements, selecting control strategies, and implementing feedback loops to maintain output quality. Good control system design ensures that processes can adapt to changes quickly and efficiently, minimizing downtime and maximizing output.
PID controllers, which stand for Proportional-Integral-Derivative controllers, are widely used in industrial applications to maintain the desired output level of a system. They are particularly effective in temperature control systems and process automation. By adjusting control inputs based on real-time feedback, PID controllers help in achieving stability and accuracy in industrial processes.
Emerging technologies in system control, such as model predictive control and adaptive control, are further enhancing industrial processes. These technologies enable systems to anticipate changes and adjust controls accordingly, improving efficiency and reducing waste. The integration of AI and machine learning with control systems is also paving the way for smarter and more responsive manufacturing solutions.
Maintenance and Safety
Maintaining electronic equipment is vital to ensuring uninterrupted operations in industrial environments. Best practices for maintaining electronic equipment include regular inspection, preventive maintenance, and timely upgrades of software and hardware components. Implementing a robust maintenance schedule helps in minimizing the risk of equipment failure and extending its lifespan.
Safety standards in industrial electronics are critical for safeguarding personnel and equipment. Compliance with regulations and standards such as IEC, UL, and OSHA ensures that electronic equipment operates safely and reliably. Regular training and certification for employees regarding safety protocols are also essential to prevent accidents and ensure a safe working environment.
The impact of the Internet of Things (IoT) on equipment maintenance is significant, as IoT technologies enable predictive maintenance strategies. By harnessing data from connected devices, industries can analyze equipment performance and predict potential failures before they occur, allowing for timely interventions and reducing downtime significantly.
Energy Efficiency
Technologies for improving energy efficiency in industrial processes include variable frequency drives, energy management systems, and advanced lighting solutions. These technologies are essential for optimizing energy use, reducing operational costs, and minimizing environmental impact. Manufacturers are increasingly adopting these technologies to enhance the sustainability of their operations.
Electronic equipment plays a pivotal role in energy management. With advanced monitoring and control systems, industries can track energy usage in real-time, leading to better resource allocation and efficiency. This proactive approach enables businesses to identify wasteful practices and implement corrective measures swiftly.
The impact of energy-efficient designs on manufacturing is profound. By optimizing energy consumption, manufacturers not only save on operational costs but also contribute to environmental sustainability. The transition towards energy-efficient systems fosters innovation and positions companies competitively within the industry.